Application
-
Power supply
-
Intelligence
-
Vehicle electronics
-
Medical care
-
Rail transit
-
Home appliances
-
Illumination
- Scan QR code
WeChat
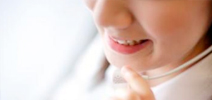
- +86 18028688880
- +86 0755-28102519
- +86 0755-28102529
- winnertong@ysxdz.com
- No.201 of Longsheng Science Building in Longsheng industry district, Dalang, Longhua, Shenzhen, China
Application of DC DC Power Module in Embroidery Machine Control System
Source:Shenzhen Yushuoxin Electronic Co., LtdTime:2017-02-28
Industrial embroidery machine commonly known as computer embroidery machine, is the most advanced contemporary embroidery machinery, with the microelectronics, computer technology, precision machinery development and application of the gradual development of mature a high degree of automation, high production efficiency of light, machine , Electric technology combined with embroidery equipment. Embroidery machine is through the control of the spindle motor and stepper motor coordination with the work, in accordance with the pattern data to form stitch to complete the embroidery. Control system as a computer embroidery machine core components, need to be equipped with stable and reliable power supply program to ensure the normal operation of the control system. Taiwan Crystal Electronics to provide customers with highly reliable, high-performance power products to help customers solve the control system in the power supply design problems, the system design more flexible and simple.
introduction
China's textile industry has a long history, after joining the WTO is to become the world's first textile production power, which gives the embroidery industry has brought a broad space for development. Embroidery machine is with the development of electronic technology and mechanical and electrical integration technology and gradually developed embroidery equipment, which makes the traditional hand embroidery to achieve high speed, high efficiency, and also meet the manual embroidery can not achieve the "multi-level, multi- Unity and perfection "requirements.
1. Computer embroidery machine works
The basic function of computer embroidery machine is through the control of the motor with the work together in the fabric in accordance with the pattern data to form a stitch to complete the embroidery process. The pattern file can be copied to the memory inside the control system through the storage medium such as the floppy disk, the U disk and so on. The control system controls the motor and its testing mechanism according to the pattern requirements, so that it can work together to complete the embroidering function. Embroidery machine work, the spindle motor through the drive wheel to drive the needle bar up and down movement, and the X-axis and Y-axis stepper motor drive the embroidery frame in the X, Y-axis movement, embroidery with embroidery frame movement, thus embroidering the pattern. When you need to change the color, the main controller by changing the color of the motor rotation, through the color change mechanism to move the color change lever, will wear other colors of the needle on the needle, continue embroidery. Computer embroidery machine control system consists of the main control circuit and external equipment, the control system block diagram is as follows.
2. Application of DC / DC Power Module in Embroidery Machine Control System
Figure 2 for the embroidery machine control system power supply block diagram, the system work is as follows:
System power supply Description: AC / DC power supply output 36V voltage, respectively, to the DC / DC module, spindle motor, XY stepper motor and voltage conversion chip power supply, DC / DC module output 5V to the display, the spindle motor encoder supply, At the same time through the LDO chip into 3.3V, 1.8V voltage to the motherboard CPU power supply.
Work process: the system power, the display, encoder, spindle motor, spindle drive board through the motherboard CPU initialization after the normal work. When the user presses the operation button, the display will feedback the signal to the motherboard CPU, the CPU will accept the instruction internal processing, and then pass the processed signal to the spindle drive board, through the drive signal to control the motor rotation (direction, , The motor will pass the axis information to the encoder, the encoder will receive the feedback signal to the motor, and at the same time the signal to the CPU, spindle motor control board, to achieve control, coding, display a series of closed-loop control process.
3. DC / DC power supply in the system application requirements
First of all, the embroidery machine in the course of the work involved in a number of motor control and power supply, on the one hand in order to prevent the power supply voltage by other load equipment, need to select the isolated power supply; the other hand, the motor will start a very high voltage spikes , The need to increase the capacitance at the front of the motor to suppress the spike voltage to prevent the other bus with the bus power supply impact; the same time, because the internal motor is a coil, instant start requires a lot of starting current, power supply to provide sufficient power to start.
Second, in the embroidery process, the motor load is constantly changing, so the motor speed must be closed-loop control, the power supply requirements not only to ensure steady-state performance, in the instantaneous load dynamic changes also need to power stable and reliable work, DC / DC module should be in the big dynamic changes to ensure that the system can work steadily.
Once again, the motherboard control system after the normal start of the work, but also internal CPU initialization process, then the initialization time must ensure that other systems have been normal start, otherwise the initialization data may be read when the power is not fully activated abnormal data , So that the system has caused a malfunction.
4. Selection of DC / DC Power Module in Application of Embroidery Machine Control System
Control of the embroidery machine action related signals through the motherboard CPU port for transmission. In order to strengthen the control of anti-interference ability, the entire control system between the circuit boards are used 12V voltage to transmit communication signals, all the main control board output control signal or input to the main control board signals are optoelectronic isolation optocoupler. In order to ensure reliable isolation of the main control board and other circuits, DC / DC mains power supply generally have 1500VDC isolation voltage.
Motor and module with the same bus voltage 36V, DC / DC module selection Wide input voltage range 18-75V, with other models of motor with bus voltage (such as 36V, 48V and other voltage), as long as the AC / DC output voltage and power to meet Request can be.
Both the display and spindle motor encoders are 5V power supply, while the motherboard CPU supply voltage is 3.3V, 1.8V, select the 5V output voltage through the LDO conversion, LDO input and output low dropout can improve conversion efficiency. DC / DC power module power and load (display, encoder, motherboard CPU), the same package size we can choose from power supply range between 10W ~ 20W.
Embroidery machine working environment temperature is generally room temperature, the maximum temperature may reach 40-50 degrees, low temperature generally more than -25 degrees, but the device starts, the temperature may not rise when the lower. Therefore, it is recommended to select the -40 ~ 85 ℃ operating temperature.
According to the above application description, we recommend the use of power supply module, need to have 1500VDC isolation voltage, 18-75V input voltage range, 5V stable voltage output, 15W power output power, 40 ~ 85 ℃ operating temperature range, plus module conversion efficiency Up to 90%, do not need to install the heat sink on the module can be reliable work.
5. Summary
With the continuous development of China's textile industry, computer embroidery machine has also been more and more widely used, people on the embroidery machine function and performance will be higher and higher, the control system is the core work device, the power requirements are also more To the higher, the power must have high performance, high reliability to meet the system design requirements.
Next article:None
Previous article:None