News
- Scan QR code
WeChat
Contact
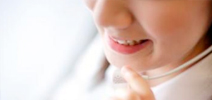
- +86 18028688880
- +86 0755-28102519
- +86 0755-28102529
- winnertong@ysxdz.com
- No.201 of Longsheng Science Building in Longsheng industry district, Dalang, Longhua, Shenzhen, China
Introduction to the basics of commonly used power devices
Source:Shenzhen Yushuoxin Electronic Co., LtdTime:2017-02-28
We
all know how to use diodes to achieve the switch, but we can only
switch on its operation, and can not gradually control the signal flow. In
addition, the diode as a switch depends on the direction of the signal
flow; we can not program it to pass or block a signal. For applications such as "flow control" or programmable switches, we need a three-terminal device and a bipolar transistor. We've all heard of Bardeen & Brattain, who accidentally invented the transistor, just like many other great discoveries.
Structurally, it is done by two back-to-back knots (this is not a big deal, as early as Bardeen, we may have used the same structure to achieve a common cathode), but in function it is completely different from the device Like a "faucet" that controls the flow of emitter currents - the "hand" of the operating faucet is the base current. The bipolar transistor is therefore a current controlled device.
Field-effect transistors (FETs), while structurally different, provide the same "faucet" function. The difference is that the FET is a voltage-controlled device; you do not need a base current, but instead use a voltage to control the current. Bipolar triode was born in 1947, shortly after a pair of outstanding father and son Shockley and Pearson invented (at least the concept) FET. In order to distinguish from the earlier bipolar "twin brother", the three electrodes of the FET are called the drain, the gate and the source, respectively. The three electrodes of the corresponding transistor are the collector, the base and the emitter pole. FETs have two major variants that are optimized for different types of applications. JFET (junction FET) is used for small signal processing, and MOSFET (metal oxide semiconductor FET) is mainly used for linear or switching power supply applications.

Why do they invent the power MOSFET?
When the bipolar transistor in proportion to the power application, it shows some annoying limitations. Indeed, you can still find them in the washing machine, air conditioners and refrigerators, but these applications are low power applications for those of us who can tolerate a certain degree of low efficiency for home appliances. Bipolar triistors are still used in some UPS, motor control, or welding robots, but their use is actually limited to applications that are less than 10KHz, and they are accelerating out of the technical frontier applications where overall efficiency becomes a critical parameter.
As a bipolar device, the transistor relies on the minority carriers injected into the base to "beat" (electrons and holes) complex and re-inject into the collector. In order to maintain a large collector current, we will inject the current from the emitter side into the base and, if possible, recover all current at the base / collector boundary (meaning that the recombination at the base must be kept to a minimum)
However, this means that when we want the transistor to be turned on, there are a large number of minority carriers with low recombination factors in the base, and the switches are processed before they are closed, in other words, with all minority carrier devices The storage charge problem limits the maximum operating speed. The main advantages of the FET are now a dawn: as most carriers, there is no storage of a small number of charge problems, therefore, its operating frequency is much higher. MOSFET switching delay characteristics are entirely due to the parasitic capacitance of the charge and discharge.
One might say that MOSFETs that require fast switching in high-frequency applications, but why should I use this device in my relatively low-speed circuit? The answer is straightforward: improving efficiency. The device has a high current and a high voltage during the duration of the switching state; since the device operates faster, the amount of energy is less. In many applications, this advantage alone is sufficient to compensate for the high turn-on loss of higher voltage MOSFETs. For example, switching mode power supplies (SMPS) at frequencies above 150 kHz can not be achieved without using it.
The bipolar transistor is driven by the current. In fact, since the gain (the ratio of the collector and the base current) decreases significantly as the collector current (IC) increases, the greater the current we are driving, The base current is also larger. A result of the bipolar transistor began to consume a lot of control power, thereby reducing the efficiency of the entire circuit.
What makes things worse is that this disadvantage will increase in the case of higher operating temperatures. Another result is the need for a very complex base drive circuit that can quickly pump and absorb current. In contrast, the current consumed by the MOS FETs at the gate is zero; even at 125 ° C, the typical gate current is less than 100nA. Once the parasitic capacitance is charged, the leakage current provided by the driver circuit is very low. In addition, voltage-driven circuits are simpler than current-driven circuits, and this is another reason why (MOS) FETs are so attractive to design engineers.
On the other hand, its main advantage is that there is no secondary damage mechanism. If an attempt is made to block a large amount of power with a bipolar transistor, the inevitable local defect in any semiconductor structure will act as a converging current and will locally heat the silicon wafer. Because the temperature coefficient of resistance is negative, the local defect will play a role in the low resistance current path, resulting in more current flowing into it, more and more heat itself, and ultimately irreversible damage. In contrast, the MOSFET has a positive resistance thermal coefficient.
On the other hand, with the increase in temperature, the increased disadvantage of RDS (on) can be perceived, and this important parameter is about doubled due to the reduced carrier mobility between 25 ° C and 125 ° C. On the other hand, this same phenomenon brings a huge advantage: any attempt to work like that mentioned above, the defects will actually divert from it - we will see the "cooling point" rather than the bipolar device "hot spots "characteristic! The equally important result of this self-cooling mechanism is to facilitate parallel MOSFETs to enhance the current performance of a device.
Bipolar triode is very sensitive to parallelism, and precautions should be taken to equalize the current (emitter stable resistance, fast response current sensing feedback loop), otherwise the device with the lowest saturation voltage will transfer most of the current, resulting in the above Overheating and eventually lead to short circuit.
Pay attention to the MOSFET, in addition to the design of insurance symmetrical circuit and the balance of the gate, they do not need other measures can be connected in parallel, so they are equally open, so that all the transistor flows through the same size of the current. In addition, the advantage lies in the fact that if the gate is not balanced and the degree of channel opening is different, this will still result in a certain drain current under steady-state conditions and slightly larger than the others.
A useful feature for the design engineer is that the MOSFET has a unique structure: there is a "parasitic" diode between the source and the drain. Although it does not optimize fast switching or low on-loss, it does not require additional cost to act as a clamp diode in an inductive load switch application.
MOSFET structure
The basic idea of JFET (Figure 1) is to control the current flowing through the drain from the source to the drain by adjusting the cross-sectional area between the drain-source channels. This can be achieved by using the inverted bias junction as a gate; its (inverted) voltage regulates the depletion region, resulting in pinch the channel and increasing its resistance by reducing its cross-sectional area. Since the gate is not applied with a voltage, the channel has the lowest resistance value and the drain current through the device is maximized. As the gate voltage increases, the beginning of the two depletion zones advances, reducing the drain current by increasing the channel resistance, and the total pinch will occur until the beginning of the two depletion zones meet.

Figure 1: JFET structure
MOSFETs use different types of gate structures to develop MOS capacitor characteristics. By changing the value and polarity of the bias applied to the top electrode of the MOS structure, you can drive it to the bottom of the chip until it is reversed. Figure 2 shows a simplified structure of an N-channel MOSFET, which is referred to as a vertical, double diffusion structure, which begins with a highly concentrated n-type substrate to minimize the bulk resistance of the channel portion.
On top of it, a layer of n-epi is grown and two successive diffusion regions are made. The appropriate bias in the p region will produce a channel, and the n + region diffused in it defines the source. Next, after forming the phosphorus-doped polysilicon, a thin, high-quality gate oxide layer is grown to form a gate. The contact window is to be opened on the top layer defining the source and gate electrodes, while the bottom of the entire wafer contacts the drain. Since there is no bias on the gate, the n + source and n are separated by the p region, and no current flows (the transistor is turned off).
If a positive bias is applied to the gate, the minority carriers (electrons) in the p region are attracted to the surface below the gate plate. With the increase of the bias voltage, more and more electrons are confined in this small space, the local "little son" concentration than the hole (p) concentration even more, resulting in "reverse" (meaning The material below the gate immediately changes from p-type to n-type). Now, n "channels" are formed in the p-type material underlying the gate structure where the source is connected to the drain; the current can flow. Just as in the case of a JFET (although the physical phenomena are different), the gate (depending on its voltage bias) controls the current between the source and the drain.

Figure 2: MOSFET structure and symbols
Many MOSFET manufacturers, almost every manufacturer has its process optimization and trademark. IR is HEXFET pioneer, Motorola built TMOS, Ixys made HiPerFET and MegaMOS, Siemens has SIPMOS family of power transistor, and Advanced Power Technology has Power MOS IV technology, and so forth. Regardless of whether the process is called VMOS, TMOS or DMOS, it has a horizontal gate structure and the current flows vertically through the gate.
The power MOSFET is unique in that it contains a plurality of "cells" as described in the parallel connection in Fig. The MOSFETs with the same RDS (on) resistance are connected in parallel with an equivalent resistance of 1 / n of RDS (on) for a MOSFET cell. The larger the die area, the lower the on-resistance, but at the same time the greater the parasitic capacitance, the worse the switching performance.
If everything is so strictly proportional and predictable, is there any way to improve it? Yes, the idea is to minimize (lower) the area of the base unit so that more units can be integrated in the same footprint space, so that RDS (on) drops and maintains the capacitance unchanged. In order to successfully improve each generation of MOSFET products, it is necessary to continuously improve the technology and improve the crystal circle manufacturing process (better line etching, better controlled perfusion, etc.).
However, continuous efforts to develop better process technology are not the only way to improve the MOSFET; conceptual design changes can greatly improve performance. This breakthrough is Philips announced in November last year: the development of successful TrenchMOS process. The gate structure is not parallel to the die surface and is now built in the channel, perpendicular to the surface, thus occupying less space and making the current flow really perpendicular (see Figure 3). In the case of RDS (on) the same, Philips's transistor to reduce the area by 50%; or, in the same current processing capacity, the area reduced by 35%.

Figure 3: Trench MOS structure
Summary of this article
We compared MOSFETs to more famous and more commonly used bipolar triodes, and we see the main advantages of MOSFETs over BJT, and we are now aware of some trade-offs. The most important conclusion is that the efficiency of the entire circuit is determined by the specific application; engineers should carefully assess the balance of conduction and switching losses under all operating conditions, and then decide which devices to use are conventional bipolar, MOSFET Or may it be IGBT?
Structurally, it is done by two back-to-back knots (this is not a big deal, as early as Bardeen, we may have used the same structure to achieve a common cathode), but in function it is completely different from the device Like a "faucet" that controls the flow of emitter currents - the "hand" of the operating faucet is the base current. The bipolar transistor is therefore a current controlled device.
Field-effect transistors (FETs), while structurally different, provide the same "faucet" function. The difference is that the FET is a voltage-controlled device; you do not need a base current, but instead use a voltage to control the current. Bipolar triode was born in 1947, shortly after a pair of outstanding father and son Shockley and Pearson invented (at least the concept) FET. In order to distinguish from the earlier bipolar "twin brother", the three electrodes of the FET are called the drain, the gate and the source, respectively. The three electrodes of the corresponding transistor are the collector, the base and the emitter pole. FETs have two major variants that are optimized for different types of applications. JFET (junction FET) is used for small signal processing, and MOSFET (metal oxide semiconductor FET) is mainly used for linear or switching power supply applications.

Why do they invent the power MOSFET?
When the bipolar transistor in proportion to the power application, it shows some annoying limitations. Indeed, you can still find them in the washing machine, air conditioners and refrigerators, but these applications are low power applications for those of us who can tolerate a certain degree of low efficiency for home appliances. Bipolar triistors are still used in some UPS, motor control, or welding robots, but their use is actually limited to applications that are less than 10KHz, and they are accelerating out of the technical frontier applications where overall efficiency becomes a critical parameter.
As a bipolar device, the transistor relies on the minority carriers injected into the base to "beat" (electrons and holes) complex and re-inject into the collector. In order to maintain a large collector current, we will inject the current from the emitter side into the base and, if possible, recover all current at the base / collector boundary (meaning that the recombination at the base must be kept to a minimum)
However, this means that when we want the transistor to be turned on, there are a large number of minority carriers with low recombination factors in the base, and the switches are processed before they are closed, in other words, with all minority carrier devices The storage charge problem limits the maximum operating speed. The main advantages of the FET are now a dawn: as most carriers, there is no storage of a small number of charge problems, therefore, its operating frequency is much higher. MOSFET switching delay characteristics are entirely due to the parasitic capacitance of the charge and discharge.
One might say that MOSFETs that require fast switching in high-frequency applications, but why should I use this device in my relatively low-speed circuit? The answer is straightforward: improving efficiency. The device has a high current and a high voltage during the duration of the switching state; since the device operates faster, the amount of energy is less. In many applications, this advantage alone is sufficient to compensate for the high turn-on loss of higher voltage MOSFETs. For example, switching mode power supplies (SMPS) at frequencies above 150 kHz can not be achieved without using it.
The bipolar transistor is driven by the current. In fact, since the gain (the ratio of the collector and the base current) decreases significantly as the collector current (IC) increases, the greater the current we are driving, The base current is also larger. A result of the bipolar transistor began to consume a lot of control power, thereby reducing the efficiency of the entire circuit.
What makes things worse is that this disadvantage will increase in the case of higher operating temperatures. Another result is the need for a very complex base drive circuit that can quickly pump and absorb current. In contrast, the current consumed by the MOS FETs at the gate is zero; even at 125 ° C, the typical gate current is less than 100nA. Once the parasitic capacitance is charged, the leakage current provided by the driver circuit is very low. In addition, voltage-driven circuits are simpler than current-driven circuits, and this is another reason why (MOS) FETs are so attractive to design engineers.
On the other hand, its main advantage is that there is no secondary damage mechanism. If an attempt is made to block a large amount of power with a bipolar transistor, the inevitable local defect in any semiconductor structure will act as a converging current and will locally heat the silicon wafer. Because the temperature coefficient of resistance is negative, the local defect will play a role in the low resistance current path, resulting in more current flowing into it, more and more heat itself, and ultimately irreversible damage. In contrast, the MOSFET has a positive resistance thermal coefficient.
On the other hand, with the increase in temperature, the increased disadvantage of RDS (on) can be perceived, and this important parameter is about doubled due to the reduced carrier mobility between 25 ° C and 125 ° C. On the other hand, this same phenomenon brings a huge advantage: any attempt to work like that mentioned above, the defects will actually divert from it - we will see the "cooling point" rather than the bipolar device "hot spots "characteristic! The equally important result of this self-cooling mechanism is to facilitate parallel MOSFETs to enhance the current performance of a device.
Bipolar triode is very sensitive to parallelism, and precautions should be taken to equalize the current (emitter stable resistance, fast response current sensing feedback loop), otherwise the device with the lowest saturation voltage will transfer most of the current, resulting in the above Overheating and eventually lead to short circuit.
Pay attention to the MOSFET, in addition to the design of insurance symmetrical circuit and the balance of the gate, they do not need other measures can be connected in parallel, so they are equally open, so that all the transistor flows through the same size of the current. In addition, the advantage lies in the fact that if the gate is not balanced and the degree of channel opening is different, this will still result in a certain drain current under steady-state conditions and slightly larger than the others.
A useful feature for the design engineer is that the MOSFET has a unique structure: there is a "parasitic" diode between the source and the drain. Although it does not optimize fast switching or low on-loss, it does not require additional cost to act as a clamp diode in an inductive load switch application.
MOSFET structure
The basic idea of JFET (Figure 1) is to control the current flowing through the drain from the source to the drain by adjusting the cross-sectional area between the drain-source channels. This can be achieved by using the inverted bias junction as a gate; its (inverted) voltage regulates the depletion region, resulting in pinch the channel and increasing its resistance by reducing its cross-sectional area. Since the gate is not applied with a voltage, the channel has the lowest resistance value and the drain current through the device is maximized. As the gate voltage increases, the beginning of the two depletion zones advances, reducing the drain current by increasing the channel resistance, and the total pinch will occur until the beginning of the two depletion zones meet.

Figure 1: JFET structure
MOSFETs use different types of gate structures to develop MOS capacitor characteristics. By changing the value and polarity of the bias applied to the top electrode of the MOS structure, you can drive it to the bottom of the chip until it is reversed. Figure 2 shows a simplified structure of an N-channel MOSFET, which is referred to as a vertical, double diffusion structure, which begins with a highly concentrated n-type substrate to minimize the bulk resistance of the channel portion.
On top of it, a layer of n-epi is grown and two successive diffusion regions are made. The appropriate bias in the p region will produce a channel, and the n + region diffused in it defines the source. Next, after forming the phosphorus-doped polysilicon, a thin, high-quality gate oxide layer is grown to form a gate. The contact window is to be opened on the top layer defining the source and gate electrodes, while the bottom of the entire wafer contacts the drain. Since there is no bias on the gate, the n + source and n are separated by the p region, and no current flows (the transistor is turned off).
If a positive bias is applied to the gate, the minority carriers (electrons) in the p region are attracted to the surface below the gate plate. With the increase of the bias voltage, more and more electrons are confined in this small space, the local "little son" concentration than the hole (p) concentration even more, resulting in "reverse" (meaning The material below the gate immediately changes from p-type to n-type). Now, n "channels" are formed in the p-type material underlying the gate structure where the source is connected to the drain; the current can flow. Just as in the case of a JFET (although the physical phenomena are different), the gate (depending on its voltage bias) controls the current between the source and the drain.

Figure 2: MOSFET structure and symbols
Many MOSFET manufacturers, almost every manufacturer has its process optimization and trademark. IR is HEXFET pioneer, Motorola built TMOS, Ixys made HiPerFET and MegaMOS, Siemens has SIPMOS family of power transistor, and Advanced Power Technology has Power MOS IV technology, and so forth. Regardless of whether the process is called VMOS, TMOS or DMOS, it has a horizontal gate structure and the current flows vertically through the gate.
The power MOSFET is unique in that it contains a plurality of "cells" as described in the parallel connection in Fig. The MOSFETs with the same RDS (on) resistance are connected in parallel with an equivalent resistance of 1 / n of RDS (on) for a MOSFET cell. The larger the die area, the lower the on-resistance, but at the same time the greater the parasitic capacitance, the worse the switching performance.
If everything is so strictly proportional and predictable, is there any way to improve it? Yes, the idea is to minimize (lower) the area of the base unit so that more units can be integrated in the same footprint space, so that RDS (on) drops and maintains the capacitance unchanged. In order to successfully improve each generation of MOSFET products, it is necessary to continuously improve the technology and improve the crystal circle manufacturing process (better line etching, better controlled perfusion, etc.).
However, continuous efforts to develop better process technology are not the only way to improve the MOSFET; conceptual design changes can greatly improve performance. This breakthrough is Philips announced in November last year: the development of successful TrenchMOS process. The gate structure is not parallel to the die surface and is now built in the channel, perpendicular to the surface, thus occupying less space and making the current flow really perpendicular (see Figure 3). In the case of RDS (on) the same, Philips's transistor to reduce the area by 50%; or, in the same current processing capacity, the area reduced by 35%.

Figure 3: Trench MOS structure
Summary of this article
We compared MOSFETs to more famous and more commonly used bipolar triodes, and we see the main advantages of MOSFETs over BJT, and we are now aware of some trade-offs. The most important conclusion is that the efficiency of the entire circuit is determined by the specific application; engineers should carefully assess the balance of conduction and switching losses under all operating conditions, and then decide which devices to use are conventional bipolar, MOSFET Or may it be IGBT?
Next article:Development and Application of Semicondu...
Previous article:None
Recommend